Il metodo 5s lean, che punta a mettere ordine e standardizzare i processi operativi e produttivi in un’ottica di miglioramento continuo dell’azienda.
I vantaggi della produzione snella
e del metodo 5s lean in azienda
Per qualità non si intende solamente quella dei prodotti/servizi finiti ma anche quella dei processi che intervengono nella loro realizzazione/erogazione. Per costo si intende quello totale di progettazione, produzione, commercializzazione ed assistenza. Mentre per delivery si intende la consegna del prodotto/servizio entro i termini concordati e con la qualità concordata con il cliente.
Poiché una produzione snella è tirata dal cliente, i prodotti ed i servizi sono realizzati nelle giuste quantità, per tempo, nelle giuste condizioni e mantenendo alto il livello della qualità.
Per comprendere appieno l’importanza dell’adozione delle 5 S in azienda proponiamo questa riflessione: Separazione, ordine e pulizia sono possibili solo dopo che la fabbrica ha raggiunto un certo livello di eccellenza o sono le condizioni necessarie per raggiungerlo?
Per le nostre PMI cresciute spesso dal niente, forti solo di una grande idea del fondatore e della sua forza sostenuta nel tempo, la risposta può non essere scontata. Ma nel tempo le condizioni di mercato sono cambiate drasticamente: oggi spesso non è più sufficiente fare del proprio meglio e metterci il massimo dell’impegno. Oggi servono strumenti e strategie capaci di supportare le turbolenze del mercato.
Il punto di partenza per raggiungere un certo livello di eccellenza è l’introduzione di metodi che mirano al miglioramento delle performance operative attraverso l’ottimizzazione l’ottimizzazione degli standard di lavoro: la metodologia 5 S racchiude tutto questo.
Le 5 S sono il primo passo verso la “Fabbrica Visuale” e sono la base per le successive attività di miglioramento.
Vediamo uno ad uno i benefici dell’applicazione del metodo:
- Sicurezza: l’applicazione delle 5 S rende il posto di lavoro più sicuro;
- Ergonomia: la disposizione di attrezzature e materiale risulta migliore;
- Qualità: migliora il processo e di conseguenza il prodotto;
- Risorse: si favorisce la comunicazione e quindi il coinvolgimento;
- Spazio: niente occupa più volume della disorganizzazione.
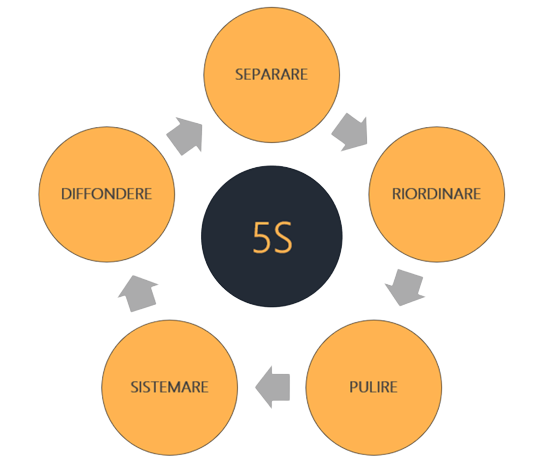
Non è snella l’azienda che taglia in modo sistematico e indiscriminato spese e consumi diretti, bensì quella che, dopo aver individuato con chiarezza il valore per il cliente, focalizza su di esso i prodotti, i processi, le risorse e l’organizzazione in modo da attuare solo azioni e investimenti efficaci, eliminando invece quelli che non creano valore aggiunto.
Cos’è il metodo 5 S?
E’ un programma di attuazione dei principi 5 S che aiuta l’azienda a raggiungere l’eccellenza operativa tramite il miglioramento del posto di lavoro: ordine, organizzazione e pulizia. Trattasi di attività semplici ma non banali e scontate.
L’applicazione delle 5 S coinvolge l’intera fabbrica mediante una serie di attività pratiche sul posto di lavoro.
Ecco alcune linee guida che possiamo definire dei veri e propri “trucchi del mestiere” per introdurre e applicare nel modo corretto la metodologia:
- L’approccio è sia dall’alto (top-down) che dal basso (buttom-up)
- La comunicazione dell’avvio di un 5 S training va fatta attraverso un momento formale in cui tutto il personale è invitato a partecipare.
Il sistema o metodo 5 S si realizza seguendo cinque fasi distinte e sequenziali Seiri, Seiton, Seiso, Seiketsu, Shitsuke.
Requisiti per applicare la metodologia 5 S
L’organizzazione ed il lavoro di squadra sono alla base del successo di questa metodologia.
Le 5 S Lean Aziendale si realizzano con il contributo di tutti (operai, capo produzione, tempi e metodi, progettazione…) ma è fondamentale stabilire delle precise responsabilità per garantire la corretta applicazione.
Gli attori principali sono:
- Responsabile della sicurezza: ricorda le regole di sicurezza, dà il via e lo stop alle attività e vigila che tutto sia a posto alla fine di un cantiere.
- Animatore: recupera tutte le segnalazioni di anomalia attraverso cartellini, e si occupa di trasmettere le informazioni ai reparti di competenza.
- Fotografo: garantisce la “memoria” di quello che era l’area prima di implementare le 5 S.
In questo processo occorre assegnare le responsabilità ponendo particolare attenzione al ruolo dell’animatore, che deve essere il riferimento per tutto il team.
Benefici del metodo 5 S sulla Lean Aziendale
Criterio guida, da considerarsi alla base per l’implementazione del Toyota Production System (TPS), è il metodo delle “5 S” (cinque “s”) che permette una gestione più ordinata e standardizzata della postazione di lavoro, l’incremento della sicurezza, la riduzione del tempo di ricerca degli oggetti, il miglior utilizzo degli spazi ed una migliore visione dal punto di vista d’immagine e comunicazione. L’obiettivo di questa metodologia è la visual management, ovvero la definizione e l’implementazione dei sistemi di gestione a vista per la diffusione ed il controllo della fabbrica.
Il metodo 5 S vede le proprie origini all’inizio degli anni Novanta, grazie a due guru giapponesi del Lean Thinking (pensioro snello), Takashi Osada e Hiroyuki Hirano.
Il termine 5 S deriva da cinque tappe:
- Seiri: separare il necessario dal superfluo, eliminando tutto ciò che non viene usato.
- Seiton: ordinare e organizzare, disponendo in modo efficiente ed ordinato ogni cosa “un posto per ogni cosa e ogni cosa al suo posto”.
- Seison: pulire e controllare le postazioni, le apparecchiature e gli attrezzi di lavoro in modo da cogliere eventuali anomalie.
- Seiketsu: standardizzare e migliorare le procedure di lavoro, l’organizzazione e le attività di pulizia creati.
- Shitsuke: sostenere il miglioramento continuo con audit sistematici per monitorare il livello raggiunto e per l’individuazione di nuovi obiettivi.
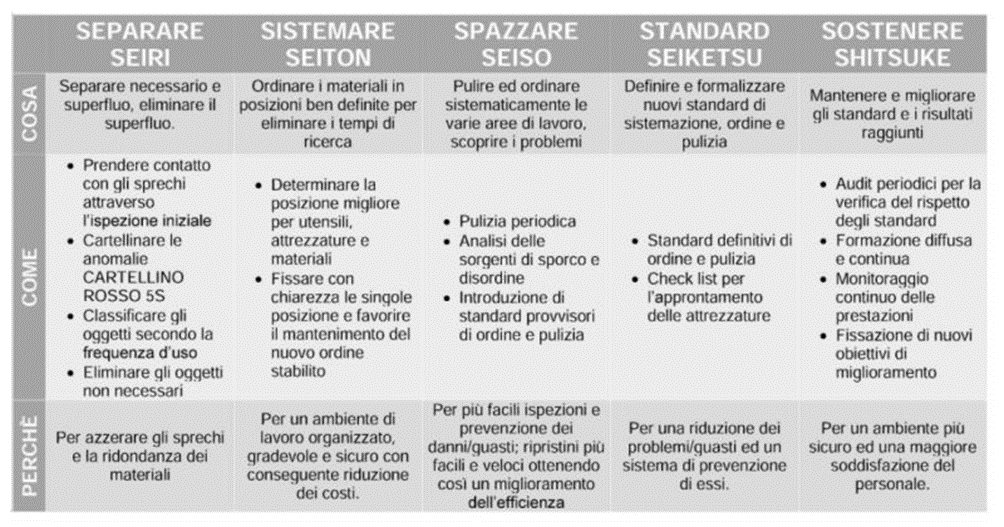
Se nel Gemba (termine giapponese per definire il luogo dove si crea valore) non vi è traccia di 5s l’azienda sarà con tutta probabilità segnata da inefficienza, scarsa autodisciplina, scarsa qualità e difficoltà nel rispettare i termini di fornitura convenuti con i clienti.
Come attivare un percorso 5S Lean in azienda a misura di PMI
Per quanto il principio alla base del metodo 5s sia semplice (ridurre tutti gli sprechi per aumentare gli utili, migliorando le performance verso i clienti) lo stesso Tahichi Ono della Toyota da cui il metodo prende forma, ha lavorato per tutta la sua vita professionale alla messa a punto di strumenti e metodi efficaci. E il suo lavoro è continuato negli ultimi 60 anni nelle più grandi aziende e multinazionali di tutto il mondo.
Ma le dinamiche di una multinazionale sono molto diverse dalle dinamiche operative, relazionali, finanziarie di una PMI italiana.
A questo punto ci sono due strade:
STRADA N°1. Cercare di fare da te. Leggi o fai leggere ad uno dei tuoi responsabili o manager quello che segue, altri post nel web che parlano dall’argomento, qualche libro sulle 5S e magari un corso in aula. Si tratta di una strada certamente fattibile ma naturalmente non semplice.
STRADA N°2. Affidarsi a chi, come noi, ha fatto dell’aiutare le PMI ad ottimizzare i costi, riorganizzare la produzione, trovare vie di innovazione fattibili e a misura delle esigenze di una PMI, anziché di grandi multinazionali o grandi aziende in cui, tipicamente vengono applicati i principi del Lean Thinking.
Metodo 5S: approfondimento tecnico
Vediamo di seguito più nel dettaglio i 5 punti che formano il metodo 5S. Come vedrai, al di là dei termini giapponesi, i concetti sono apparentemente molto semplici. La cosa difficile sta nell’applicarli in modo integrato, non invasivo e soprattutto efficace, all’interno della tua azienda, senza sovraccaricare con procedure inutili e attività che fanno perdere tempo, anziché guadagnarne.
Punto 1 Metodo 5s: SEIRI – Separare
“Perdita è tutto ciò che eccede il minimo necessario in attrezzature, spazio e tempo! In caso di dubbio, eliminare”
La prima fase consiste nell’eliminare qualsiasi cosa che non serve nella postazione di lavoro.
L’attività lavorativa quotidiana porta ad accumulare molti oggetti, materiali e strumenti inutilizzati che occupano solo spazio. L’obiettivo è individuarli mettendo in discussione il loro stesso impiego.
A livello pratico si utilizza l’applicazione di un cartellino rosso:
- Effettuare una fotografiadella situazione attuale con lo scopo di poter fare un confronto con la situazione finale e comprendere cosa è cambiato.
- Creare un team multifunzionale, composto da persone provenienti dai reparti produttivi, dalla logistica, dalle funzioni indirette. La presenza di almeno una figura di alto livello è molto importante per la risoluzione immediata delle anomalie.
- Determinare il reparto o l’impianto oggetto di analisi.
- Determinazione del criterio di selezione degli oggetti “che cosa serve o non serve”. Avrà il cartellino rosso ciò che non è stato utilizzato nell’ultimo mese, ciò per cui non c’è in programma l’utilizzo entro il prossimo mese.
- Applicare i cartellini rossi. Il team di progetto assieme al responsabile di produzione fanno i giri d’ispezione nel reparto valutando in modo oggettivo l’utilizzo dei vari strumenti. Durante questa fase si propone anche il “futuro” dell’oggetto: la ricollocazione, ovvero lo strumento si trova in un luogo non consono ma è utile al reparto e sarà necessaria la collocazione opportuna, oppure l’eliminazione, cioè il team ritiene superflua la presenza dell’oggetto nel reparto.
- Prendereprovvedimenti nei confronti degli oggetti evidenziati con i cartellini rossi. Si stende un elenco degli oggetti non necessari (per tenere una traccia), i provvedimenti da prendere vengono decisi e successivamente implementati.
- Analizzarei risultati ottenuti.
Nel separare gli oggetti bisogna ricordarsi dell’atteggiamento del “perché”. Molti strumenti sono presenti perché “un giorno potrà essermi utile”, ma nessuno monitora quando questo momento effettivamente si verifica e se si verifica. È necessaria una oggettività nel valutare il reale utilizzo di ogni oggetto.
Check List 5S: Seiri – Separare
- Ci sono materiali, strumenti, macchinari o documenti non utilizzati?
- Cos’è questo materiale, strumento, macchinario o documento?
- Chi lo usa?
- Quando è stato utilizzato l’ultima volta?
- Perché viene utilizzato?
- È stato individuato da più di una settimana?
- Esiste una procedura per eliminarlo?
- Ci sono materiali o strumenti che possono intralciare il lavoro?
- Gli oggetti dichiarati utili sono catalogati, disposti ordinatamente ed, eventualmente, etichettati?
- Quali sono stati gli oggetti dichiarati “inutili”?